Lean Six Sigma Training
Our Continuous Improvement (CI) training courses are project-based, ensuring that every attendee will solve a real business problem while building capability in the methodology. We tailor our courses to your business and your problems, teaching those concepts that will be most useful for the problems you face. Training is just the first step: we also provide coaching and certification in Lean Six Sigma techniques. Learn more about Lean Six Sigma methodology below...
Introduction to Continuous Improvement (Simulation)
Get started with Continuous Improvement through an interactive, engaging workshop using a process simulation. Each participant has a role to play in a process that doesn't work very well at the start. Learning and applying Lean Six Sigma techniques to improve the process, the team will achieve a breakthrough in reducing process cycle time, eliminating defects, and delighting the customer. The simulation works best for groups of 12 and above. For groups of 25 and up, we can run multiple sims side by side, increasing competition and excitement as each team tries to to better than the other(s).
Introduction to Continuous Improvement
For smaller groups or tighter time constraints, we can provide an introduction to CI in a shorter session, drawing up on the experiences of the group to show how the tools and methods apply to the problems they face.
This type of session is easily customised to the specific context of your organisation, with flexibility around the preferred language, methods, and messages you want to deliver.
Executive
Establish the vision, strategy, and measures of success, engaging senior leadership to prepare them for their leadership role as drivers of your Continuous Improvement deployment. Without the active support of senior leaders, any company initiative is unlikely to succeed. This session ensures the leadership is aligned around shared goals, and helps them to understand the different behaviours necessary to change the way their teams approach problems.
Champion (Sponsor)
Set the stage for success with project sponsors, understanding Lean Six Sigma terminology, project identification & selection, project charters, supporting infrastructure, project reviews, communications and rewards. Sponsors have to make the day to day decisions on how projects are prioritised and resources are allocated. This session prepares them to actively sponsor one or more projects and to understand the challenges they, and the project leaders, will face, and how to respond to ensure success.
Yellow Belt
Learn the basics of continuous improvement techniques such as writing good problem statements, engaging stakeholders, mapping a process and identifying waste, brainstorming solutions, and ensuring they are sustainable.
Green Belt
Build on the learning from Yellow Belt training with techniques including Voice of Customer, sampling, graphical analysis, process analysis, basic hypothesis testing, solution implementation and statistical process control.
Black Belt
Develop full competency in Lean Six Sigma, strengthening stakeholder engagement capability, statistical analysis, hypothesis testing, designed experiments, and statistical process control.
Master Black Belt
Become an expert in Lean Six Sigma, addressing personal development needs in deployment, engaging leadership, training other Belts, and advanced statistical techniques.
Learn how to create a new product or process using Design for Six Sigma principles, ensuring the new process meets customer requirements from day one.
TRIZ
Apply structure to innovation and creativity using the Theory of Inventive Problem Solving, with techniques including Ideal Final Result, the Contradiction Matrix, and the 40 Principles of Problem Solving.
CI Coach
Practice how to be a better coach, including workshop facilitation, one-on-one coaching, providing feedback, and teaching & facilitating the Continuous Improvement tools. Sometimes the person with just a bit of CI knowledge or capability is expected to guide others in the application of CI tools and methods. This course increases the participants technical depth while also strengthening coaching and facilitation skills. The course is widely applicable to those early on in their CI journey as well as more seasoned Black Belts or Master Black Belts who want to further develop their soft skills.
Customised Training
In most cases our training courses are tailored to your company, culture and challenges. We also offer customised courses in specific techniques, or interactive workshops that combine learning and project execution. Learn more about Problem Solving Workshops and Rapid Improvement...
Lean Six Sigma is a combination of the principles of Lean and the structured problem solving approach of Six Sigma. They are part of a general approach to Continuous Improvement: using the most appropriate approach, method or tool at the right time to understand and solve problems. A Rapid Improvement workshop can enhance engagement while applying these principles to achieve fast results. All these methods are most effective when coupled with Change Acceleration to manage the human side of change.
What is Lean?
.png)
The principles of Lean are targeted at identifying and eliminating waste in all its forms. They were developed in Japan in the post-World War II era, primarily by Toyota Motor Corporation, and articulated in this form by Womack and Jones in their 1996 book, Lean Thinking.
- Value: Recognise what the customer perceives as Value; what are they actually paying for?
- Value Stream: Identify the interconnected activities and relationships that directly produce that value
- Pull: Produce only what the customer needs when they need it: all activities at a step are initiated by the subsequent step (all the way to the customer)
- Flow: Minimise or eliminate the delay between value-added steps
- Perfection: Apply continuous improvement to ensure things are always done right the first time
What is Six Sigma?
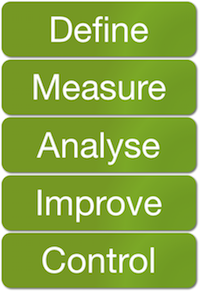
The Six Sigma methodology is focused on ensuring processes meet customer requirements by eliminating defects and reducing variation. Six Sigma was developed in the 1980s by Motorola, and made popular in the 1990s by General Electric. This approach is most effective for improving existing processes. Practitioners of Six Sigma typically become certified according to their level of capability, experience and project delivery.
- Define: Clearly define the problem; gather the Voice of Customer; map the process at a high level; determine potential project value
- Measure: Gather the data to determine the actual performance (baseline); map the value stream; perform a process risk assessment; measure waste and Cost of Poor Quality; implement Quick Wins
- Analyse: Use data and statistics to identify and validate root causes; perform Value analysis to uncover bottlenecks, delays and other waste
- Improve: Implement improvements targeted to root causes; eliminate waste and variation; demonstrate measurable improvement (practically and statistically)
- Control: Ensure sustainability of the process; measure stability using Statistical Process Control, Standard Work and visual management
The Design for Six Sigma (DFSS) approach is used to create a new product or process, or to significantly redesign the existing one. The five phases of DMADV help you to define the opportunity, understand the detailed stakeholder needs, generate design concepts, develop and optimise the design, and validate adherence to customer requirements.
- Define: Clearly define the opportunity; gather the Voice of Customer (value, wants, needs, requirements); determine project boundaries
- Measure: Identify detailed stakeholder needs; quantify metrics and specifications; perform benchmarking; develop design scorecard
- Analyse: Identify and prioritise key functions; develop function structure; generate design concepts; perform risk analysis
- Design: Define design elements and requirements; develop detailed design; simulate, refine, and optimise design for robustness
- Verify: Pilot and implement design; monitor outputs, control inputs; validate adherence to customer requirements; transfer control